CASE STUDY
Industry: Logistics / Material Handling
Product: Helios2 Time-of-Flight Camera
Software: Arena SDK & customized AI algorithms
Automated AI-Driven Depalletizer Powered by
Helios2 Time-of-Flight Camera
Optimizing distribution and logistics processes is an ongoing challenge across many industries, which is driven by the need to improve ergonomics, traceability, and product quality. Traditional manual methods of unloading pallets often entail repetitive tasks that add little overall value, leading to increased operational costs and potential quality issues. To address these challenges, many warehouses have embraced automated solutions such as mobile depalletizers to increase efficiency and throughput rates.
Challenge
A large warehouse in Spain faced the challenge of efficiently unloading pallets stacked with cardboard boxes of varying sizes and weights. The weight of these boxes could make them collapse, and therefore it required a way to automatically identify the box types, sizes, and where they were located so that they could be unloaded correctly.
This challenge had several dimensions, including the need to enhance ergonomics, traceability, and product quality. Doing this task manually was not only repetitive but also prone to human error, which could lead to damage and losses. The primary obstacle was developing a system adaptable to a diverse range of box types and shapes, achieved through AI algorithms trained on a variety of boxes and the utilization of depth and intensity images using 3D Time-of-Flight technology.
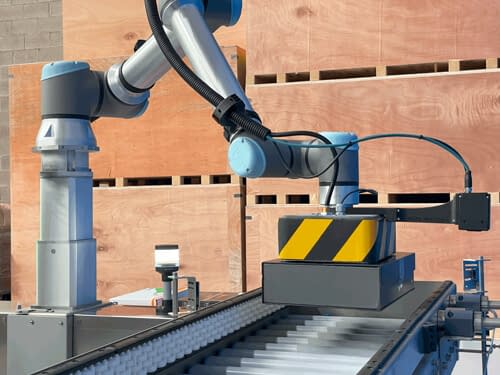
Solution
Inser Robotica , an engineering company based in Spain, was tasked to develop an automated solution featuring a universal depalletizer capable of handling multi-format boxes. Collaborating with ClearView Imaging, a leading machine vision component supplier, they integrated an advanced 3D Time-of-Flight (ToF) camera technology into the system, resulting in exceptional precision, high throughput rates, and full autonomy for the unloading process.
LUCID’s Helios2 ToF camera played a pivotal role in achieving precise box segmentation and coordinate calculation by generating a point cloud of the boxes and packages on the pallet’s top layer. AI-driven software then identified each box’s position and coordinates, strategically determining the optimal unloading sequence. Helios2’s ToF technology featuring the Sony DepthSense IMX556 CMOS sensor proved superior in capturing images swiftly, accurately, and reliably compared to other 3D camera technologies.
To seamlessly integrate the Helios2 camera, Inser Robotica designed a dedicated support structure for mounting it onto the robot. This ensured optimal camera positioning for pallet capture and robot coordination. Inser Robotica used their custom software that simplified camera and robot calibration, streamlining the startup process.
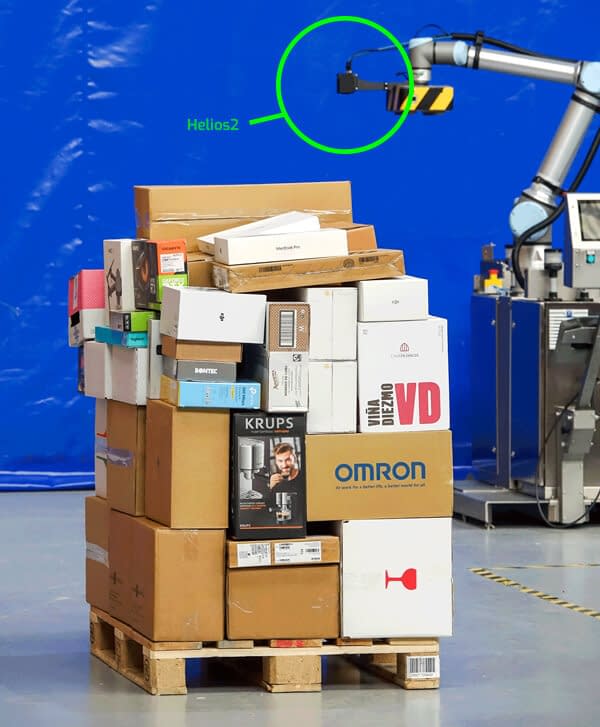
Inser’s depalletizer is equipped with a Helios2 3D Time-of-Flight camera, which provides 3D point cloud data used to identify the position of boxes and packages.
Utilizing LUCID’s Helios2 3D ToF camera offered several key advantages. “Its affordability made our solution economically competitive without compromising on the precision and reliability requirements essential for these systems”, says Antxoka Gómez, CMO at Inser Robotica. “LUCID’s ArenaView software has been instrumental in configuring the camera and optimizing image preprocessing to adapt to varying lighting conditions. Additionally, the camera’s IP67 protection allowed us to deploy installations in challenging, dusty, and humid environments without compromising performance.”
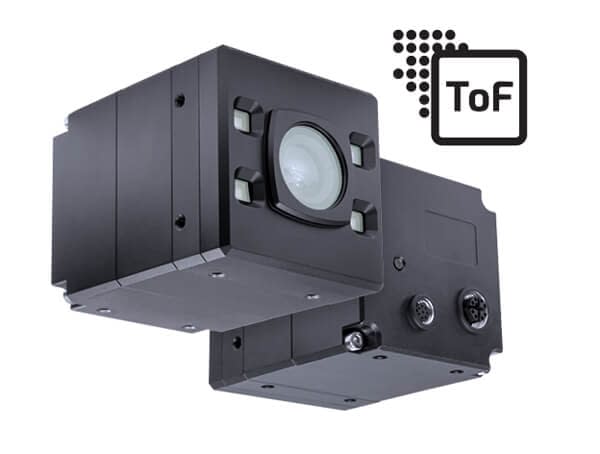
The IP67 Helios2 ToF camera features Sony’s DepthSense IMX556 CMOS sensor, delivering sub-millimeter precision and high accuracy.
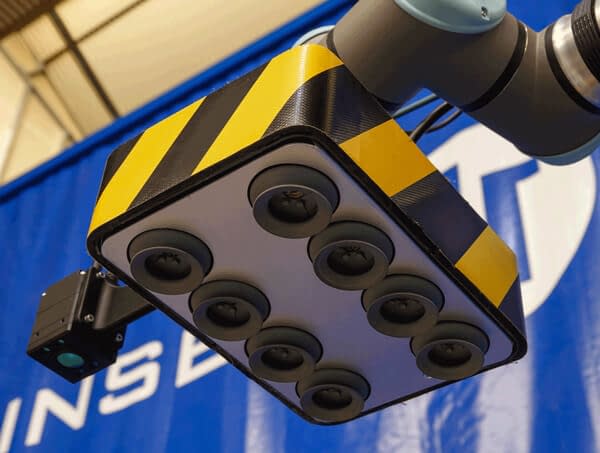
The camera’s IP67 protection allows for reliable operation in challenging, dusty, and humid environments without compromising performance.
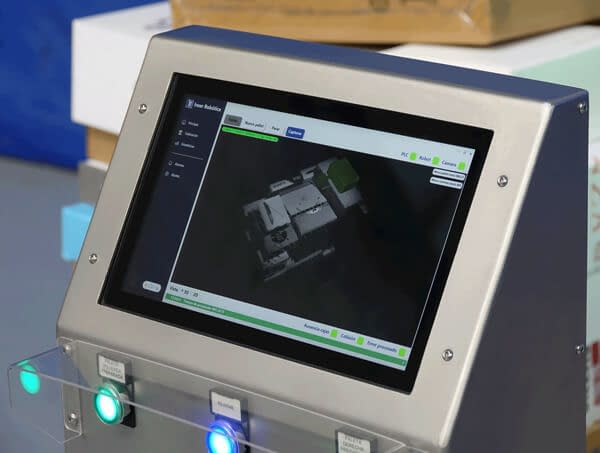
Helios2 generates a point cloud of the boxes and packages on the pallet’s top layer. AI-driven software then identifies each box’s position and coordinates, and can determine the optimal unloading sequence.
Conclusion
The integration of Inser Robotica’s automated depalletizer, featuring LUCID’s Helios2 camera, brings significant advantages to end customers in logistics and distribution. It achieves high and unattended throughput, resulting in substantial cost savings, reduced labor expenses, and minimized supervision requirements. Furthermore, the solution mitigates costly errors such as product loss or misplacement during the unloading process, preserving product quality and financial performance. In essence, the incorporation of automated AI-driven robot technology not only streamlines operations but also empowers end customers to enhance their competitiveness and operational excellence in the logistics and distribution sectors.
See a video of Inser’s robotic AI driven depalletizer in action.